Understanding the Role of a Solvent Extraction Plant
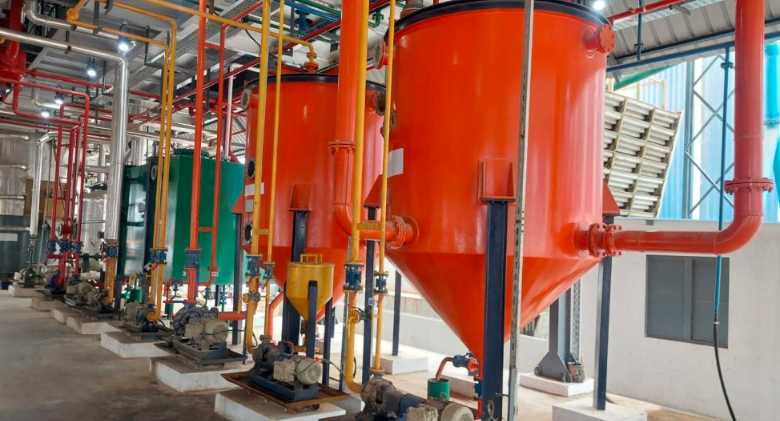
A solvent extraction plant is an industrial facility used to extract valuable components from raw materials using a chemical solvent. This process is widely applied in industries such as oilseed processing, pharmaceutical production, and metal refining. It offers high efficiency and cost-effectiveness, making it a preferred method for extracting oils, metals, and bioactive compounds.
This article explores the working principles of a solvent extraction plantits applications, benefits, and challenges.
What is a Solvent Extraction Plant?
A solvent extraction plant is designed to separate specific compounds from solid or liquid mixtures using a solvent. The solvent selectively dissolves the desired component, leaving behind unwanted materials. The extracted component is then recovered, and the solvent is often reused in a closed-loop system.
This method is commonly used in:
- Vegetable oil production (extracting oil from seeds like soybean, sunflower, and rapeseed)
- Pharmaceutical industry (isolating active compounds from plants)
- Metal extraction (separating valuable metals from ores and industrial waste)
How a Solvent Extraction Plant Works
The solvent extraction process involves several key steps to ensure the efficient separation of targeted compounds. Below is a breakdown of the process:
1. Preparation of Raw Material
Before extraction, the raw material undergoes pre-processing, which may include:
- Grinding or crushing (for seeds and ores)
- Drying to remove excess moisture
- Heating (in some cases) to improve extraction efficiency
2. Solvent Selection and Application
A suitable solvent is chosen based on the properties of the target compound. Common solvents include:
- Hexane: Used in vegetable oil extraction
- Ethanol: Common in herbal and pharmaceutical extractions
- Kerosene or Diluted Acids: Used for metal extraction
The raw material is then soaked or mixed with the solvent to dissolve the desired component.
Read also: Keys to Preparing Your Business for Emergencies
3. Separation and Filtration
Once the solvent has absorbed the target compound, the mixture is filtered or centrifuged to separate solid residues. This step ensures that only the solvent and dissolved component remain.
4. Solvent Recovery and Purification
The solvent and extracted material are then separated using methods such as:
- Evaporation: Heating the mixture to remove the solvent
- Distillation: Separating components based on boiling points
- Precipitation or Crystallization: Allowing the extracted substance to form solid crystals
After recovery, the solvent is purified and reused to improve efficiency and reduce costs.
5. Final Processing of Extracted Material
The extracted compound may undergo further refining, drying, or blending before being packaged for use in industries like food processing, pharmaceuticals, and metal manufacturing.
Applications of a Solvent Extraction Plant
1. Vegetable Oil Industry
One of the most common uses of solvent extraction plants is in oilseed processing. The plant extracts oils from seeds such as:
- Soybean
- Sunflower
- Cottonseed
- Canola
This method ensures maximum oil yield while maintaining quality.
2. Pharmaceutical and Herbal Extracts
In the pharmaceutical industry, solvent extraction is used to isolate bioactive compounds from medicinal plants. It is commonly applied in the production of:
- Essential oils
- Herbal medicines
- Pharmaceutical drugs
3. Metal and Mineral Extraction
The solvent extraction process is crucial in mining and metallurgy. It helps separate valuable metals such as:
- Copper
- Uranium
- Gold
This method ensures efficient metal recovery with minimal waste generation.
4. Food and Flavoring Industry
Solvent extraction is also used to obtain:
- Natural flavors and colorants from plant sources
- Caffeine from coffee beans
- Aromatic compounds for perfumes
This technique preserves the natural essence of extracted materials.
Advantages of a Solvent Extraction Plant
1. High Efficiency and Maximum Yield
Compared to mechanical pressing, solvent extraction provides a higher yield of the desired compound. This makes it a cost-effective solution for large-scale production.
2. Consistent Quality
Solvent extraction ensures uniform composition and purity, making it ideal for industries requiring precise formulations.
3. Reduced Waste and Environmental Impact
By optimizing extraction efficiency, solvent extraction plants minimize raw material waste. Additionally, many facilities implement solvent recycling systems to reduce environmental pollution.
4. Lower Production Costs
Since solvent extraction achieves higher yields, industries benefit from reduced raw material costs. Solvent recovery systems further enhance cost savings.
5. Versatility in Applications
A solvent extraction plant can be adapted for various industries, making it a flexible and valuable processing technology.
Challenges in Solvent Extraction
1. Solvent Handling and Safety
Many industrial solvents are flammable or toxic. Strict safety measures must be in place to prevent fire hazards, health risks, and environmental pollution.
2. Solvent Residue in Extracted Products
Ensuring that the final product is free from residual solvents is critical, especially in food and pharmaceutical applications. Advanced purification techniques are required to meet regulatory standards.
3. High Initial Investment
Setting up a solvent extraction plant requires significant capital investment in equipment, safety infrastructure, and compliance measures. However, long-term operational savings offset these costs.
4. Regulatory Compliance
Industries must comply with strict environmental and safety regulations governing solvent use, storage, and disposal. Regular audits and monitoring are essential.
Future Trends in Solvent Extraction
With growing environmental concerns and advancements in technology, solvent extraction plants are evolving. Some key trends include:
1. Use of Green and Bio-Based Solvents
Industries are shifting toward eco-friendly solvents such as water-based or plant-derived alternatives to reduce environmental impact.
2. Automation and AI Integration
Modern solvent extraction plants are incorporating AI-driven monitoring systems to optimize efficiency, reduce human errors, and enhance safety.
3. Hybrid Extraction Techniques
Combining solvent extraction with other methods like supercritical fluid extraction improves efficiency while maintaining product purity.
4. Improved Solvent Recovery Systems
Advanced distillation and membrane technologies are being developed to increase solvent recovery rates, making the process more sustainable.
5. Expansion into New Industries
Beyond traditional applications, solvent extraction plants are being explored for extracting biofuels, biodegradable plastics, and rare earth metals.
Conclusion
A solvent extraction plant plays a crucial role in industries ranging from food production to mining. This technology offers high efficiency, cost savings, and minimal waste generation. Despite challenges such as solvent safety and regulatory compliance, advancements in green chemistry and automation are making solvent extraction more sustainable and reliable.
As industries continue to prioritize resource optimization and environmental responsibility, solvent extraction plants will remain a vital part of modern manufacturing and processing systems.