Precision in Oil and Gas CNC Machining
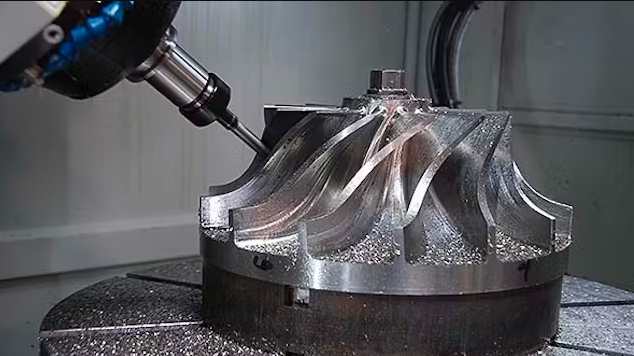
The oil and gas industry relies heavily on advanced manufacturing techniques to produce durable, high-precision components. Among these Oil and Gas CNC Machining plays a critical role in fabricating parts that withstand extreme pressure, temperature variations, and harsh operating conditions. Computer Numerical Control (CNC) machining provides accuracy, consistency, and efficiency in producing essential components used in drilling, extraction, and transportation.
This article explores the importance of oil and gas CNC machining, the materials used, the key components manufactured, and the challenges associated with this sector.
Understanding CNC Machining in the Oil and Gas Sector
CNC machining is a computer-controlled manufacturing process that precisely cuts, drills, and shapes metal or plastic materials. It is widely used in industries that demand high accuracy, such as aerospace, automotive, and medical. However, in the oil and gas sector, CNC machining is even more critical due to the harsh and demanding environments in which components must operate.
Oil and gas drilling equipment, pipelines, and valves require tightly controlled tolerances and exceptional material strength to endure pressure, heat, and corrosive conditions. CNC machining ensures that these components are manufactured to exact specifications, improving reliability and longevity.
Why CNC Machining is Essential for Oil and Gas
The oil and gas industry depends on CNC machining for several reasons:
1. Precision and Accuracy
CNC machines follow pre-programmed instructions, ensuring consistent and accurate cuts with minimal human error. This level of precision is essential for parts that must fit together perfectly in complex drilling systems.
2. Durability and Strength
Oil and gas components must endure high stress, corrosive chemicals, and extreme temperatures. CNC machining allows the use of robust materials such as stainless steel, titanium, and Inconel, ensuring durability.
3. Cost Efficiency
CNC machining reduces material waste and optimizes production efficiency. The ability to manufacture parts with tight tolerances minimizes rework and material loss, lowering overall costs.
4. Scalability
Oil and gas companies require both custom, one-off components and high-volume production runs. CNC machining can efficiently handle both, making it suitable for large-scale industrial operations.
5. Complex Geometries
Modern CNC machines can create intricate designs and complex geometries that would be difficult or impossible to achieve with traditional machining methods. This is crucial for specialized parts used in drilling and extraction equipment.
Key Materials Used in Oil and Gas CNC Machining
Selecting the right material is crucial for ensuring longevity and performance in oil and gas applications. The following materials are commonly used in oil and gas CNC machining:
1. Stainless Steel
- High resistance to corrosion and heat
- Used in valves, pumps, and pipelines
2. Inconel
- Withstands extreme temperatures and pressure
- Commonly used in turbines, exhaust systems, and downhole tools
3. Titanium
- Lightweight yet exceptionally strong
- Ideal for high-pressure pipelines and drilling components
4. Carbon Steel
- Offers strength and affordability
- Used in structural frameworks and casing systems
5. Brass and Bronze
- Resistant to saltwater corrosion
- Used in marine applications and offshore drilling rigs
CNC Machined Components in Oil and Gas
CNC machining is used to manufacture various critical components for the oil and gas industry. Some of the most important include:
1. Drill Bits
CNC machining creates high-precision drill bits capable of cutting through tough rock formations. The accuracy of CNC ensures that these bits remain sharp and durable.
2. Pump Components
Pumps play a crucial role in moving oil and gas through pipelines. CNC machining is used to produce pump casings, impellers, and seals with precise tolerances.
3. Valves and Fittings
CNC-machined valves, couplings, and flanges help regulate the flow of oil and gas. These components must be leak-proof and able to withstand high pressures.
4. Downhole Tools
Downhole tools, such as mud motors, stabilizers, and collars, require intricate machining to ensure functionality in deep drilling operations.
5. Pipeline Components
CNC machining produces custom pipeline connectors, manifolds, and reducers to ensure smooth transportation of oil and gas.
6. Blowout Preventers (BOPs)
A critical safety component, blowout preventers control pressure surges during drilling. These parts must be precisely machined to prevent failures.
7. Offshore Rig Parts
Components for offshore platforms, such as brackets, structural supports, and housings, are manufactured using CNC machining for enhanced durability.
Challenges in Oil and Gas CNC Machining
Despite its benefits, oil and gas CNC machining comes with unique challenges:
1. Tough Material Machining
Many materials used in oil and gas, such as Inconel and titanium, are difficult to machine due to their hardness and heat resistance. Specialized cutting tools and cooling techniques are required.
2. Maintaining Tight Tolerances
Even minor deviations in part dimensions can lead to operational failures. CNC machining must maintain extremely tight tolerances, sometimes within microns.
3. Harsh Environmental Conditions
Components must withstand saltwater exposure, high pressure, and chemical corrosion. This requires advanced coatings and surface treatments to improve longevity.
Read also: Why Businesses Are Investing in Animation: The Rise of Video Marketing in 2025
4. Production Costs
High-quality materials and precision machining increase costs. However, CNC machining’s efficiency helps offset these expenses over time.
5. Regulatory Compliance
The oil and gas industry follows strict regulations to ensure safety and reliability. CNC-machined parts must meet industry standards such as API (American Petroleum Institute) and ISO certifications.
Future Trends in Oil and Gas CNC Machining
As technology advances, CNC machining continues to evolve in the oil and gas industry.
1. Automation and AI Integration
Automated CNC systems and AI-driven monitoring enhance precision and reduce human errors. These technologies also improve predictive maintenance, reducing downtime.
2. 3D Printing and CNC Hybrid Manufacturing
Combining CNC machining with additive manufacturing (3D printing) allows for rapid prototyping and custom part fabrication. This hybrid approach is gaining traction in oil and gas manufacturing.
3. Advanced Coatings and Surface Treatments
New wear-resistant coatings and treatments, such as plasma nitriding and ceramic coatings, improve part longevity in extreme conditions.
4. Sustainable Manufacturing Practices
Oil and gas companies are adopting eco-friendly machining processes that reduce material waste and energy consumption, making CNC machining more sustainable.
Conclusion
Oil and gas CNC machining plays a vital role in producing high-precision components that operate in harsh environments. The industry depends on CNC machining for its accuracy, efficiency, and ability to handle tough materials. From drill bits and valves to pipeline connectors and offshore rig parts, CNC technology ensures that essential equipment meets the highest standards.
Despite challenges such as tough material machining, tight tolerances, and regulatory requirements, advances in automation, AI, and hybrid manufacturing are shaping the future of CNC machining in the oil and gas sector. By investing in advanced machining technologies, companies can improve efficiency, reduce costs, and enhance safety, ensuring long-term success in this demanding industry.